Update Januar 2023: Youtube Video zur Schalldämmung!
Schon in 2011 habe ich mich mit Schalldämmung und -dämpfung beschäftigt, damals noch auf der Xenia (Bericht hier!), die ursprünglich nur sehr wenig Schallisolierung im Maschinenraum hatte.
Die Julius war schon beim Kauf leiser als die Xenia nach meinen aufwändigen Maßnahmen zur Schalldämmung. Also, warum standen dann vor ein paar Tagen diese Matten zur Schallisolierung in unserem Wohnzimmer?
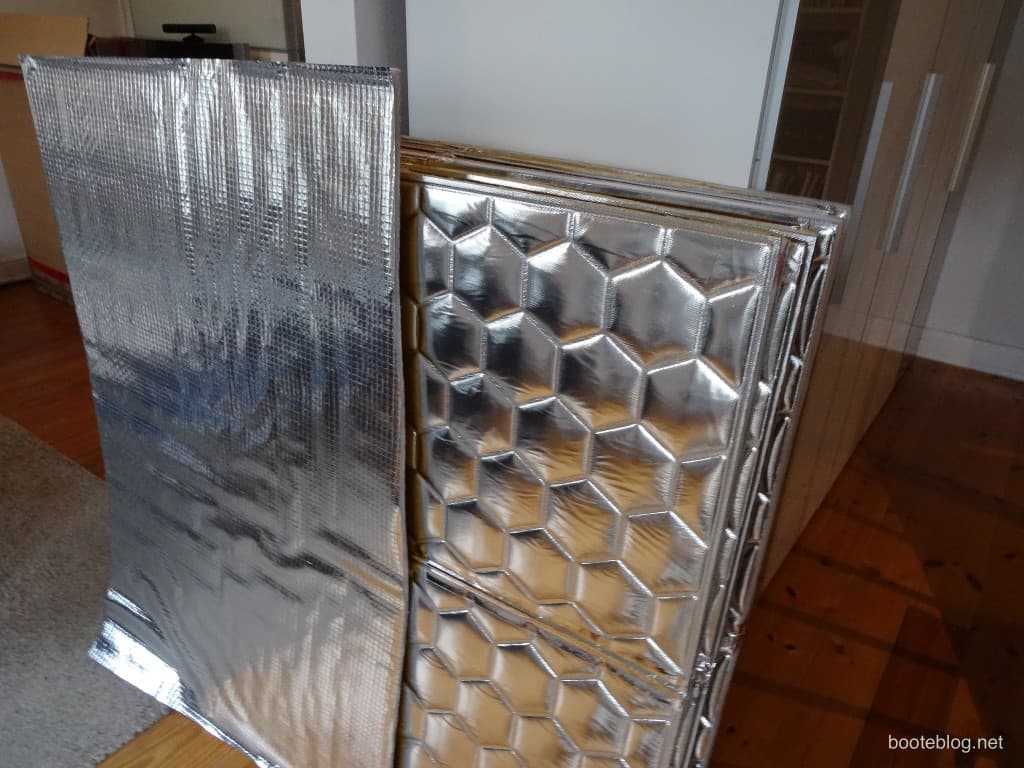
Einerseits bröckelten und bröselten einige alte Schallisolierungssplatten im Maschinenraum der Julius schon, wenn ich sie nur scharf angeguckt habe. Dieses alte Material musste also sowieso raus und ersetzt werden.
Und dann ist da noch ein kleiner Spleen, wie Engländer es vermutlich bezeichnen würden. Anderen kommen Begriffe wie „Perfektionismus“ in den Sinn, wenn sie mich über die Suche nach der perfekten Schallisolierung im Maschinenraum reden hören: Ich möchte, dass mein Motorkreuzer so leise wie mit vertretbarem Aufwand möglich ist. Meine – soviel sei vorweg gesagt – nicht ganz erfüllte Vorstellung war, noch mal eine deutliche Reduzierung des Maschinen- und Generatorgeräusches zu erreichen.
Schallisolierung im Maschinenraum: AIXFoam gegen Recytex
Bei der Xenia hatte ich Material von aixfoam.de verwendet (SH0071 in 50mm), mit dem ich sehr zufrieden war – in dem Wissen, dass es in vielen Jahren auch durch Öl- und Dieseldämpfe angegriffen sein wird.
Für die Julius habe ich aber nun ein Material mit einer belastbaren Oberfläche gesucht, erstens um eine lange Haltbarkeit zu erreichen. Und Zweitens, weil ich im Maschinenraum immer mal mit Werkzeug irgendwo gegen komme, und dabei darf das Material keinen Schaden nehmen.
Aixfoam hat auch Material mit Oberflächenkaschierung (SH0081), was aber – warum auch immer – schlechtere Werte als die SH0071 Matten hat. Und wie belastbar die Oberfläche ist, konnte ich nicht ermitteln.
Von günstigen Materialien wie dem typischen Noppenschaumstoff kann ich übrigens nur abraten: Für die Schallisolierung der Maschine ist so etwas nahezu vollständig nutzlos.
Recytex hatte ich auf der boot 2016 in Düsseldorf besucht und konnte mich von der sehr stabilen Oberfläche selbst überzeugen:
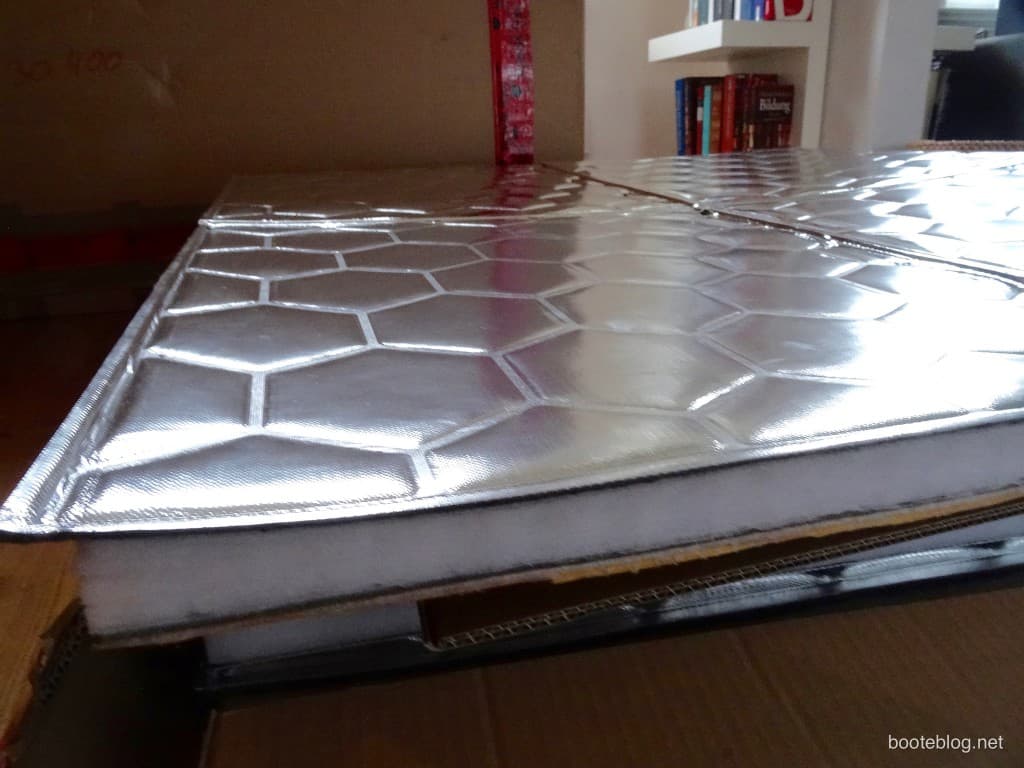
Im Einzelnen besteht das Material aus:
- Einer relativ schweren (gegen niedrige Frequenzen) und harten Schicht mit Selbstklebevorrichtung.
- Einem großvolumiges Flies (dämmt mittlere und hohe Frequenzen).
- Dann eine mittelschwere Schicht aus dichtem Flies (noch mal gegen niedrige Frequenzen).
- Schließlich die sehr stabile Oberfläche.
Dazu gibt Recytex für das W600 Material eine durchschnittliche Reduzierung des Schallpegels von 24,4dB an, davon immerhin zwischen 15dB und 20dB bei den sehr tiefen Frequenzen. Zum Vergleich: Eine Reduzierung von 3dB wird als Halbierung des Lärms empfunden. Korrektur: 3dB weniger Lärm wird nicht als Halbierung empfunden – siehe unten die Anmerkung von Michael Herrmann!
Auf der Messe stand bei Recytex als Beispiel eine Box, die von innen mit dem Material ausgekleidet war. Im Inneren der Box lagen Lautsprecher, die ein lautes Maschinengeräusch abgespielt haben. Dieser Test berücksichtigt natürlich nur den Luftschall und lässt den wichtigen Körperschall (Maschine überträgt Lärm auf den Schiffskörper) völlig außen vor. Aber: Der Unterschied zwischen der geöffneten und geschlossen Box war ganz erheblich, ganz nutzlos kann das Material also nicht sein.
Messen, Zuschneiden, Putzen, Anbringen
So kam das Recytex Material ins Haus und zur Julius. In der perfekten Welt hätte der Maschinenraum dort glatte Wände. In der echten Welt dagegen sah es im Maschinenraum so aus:
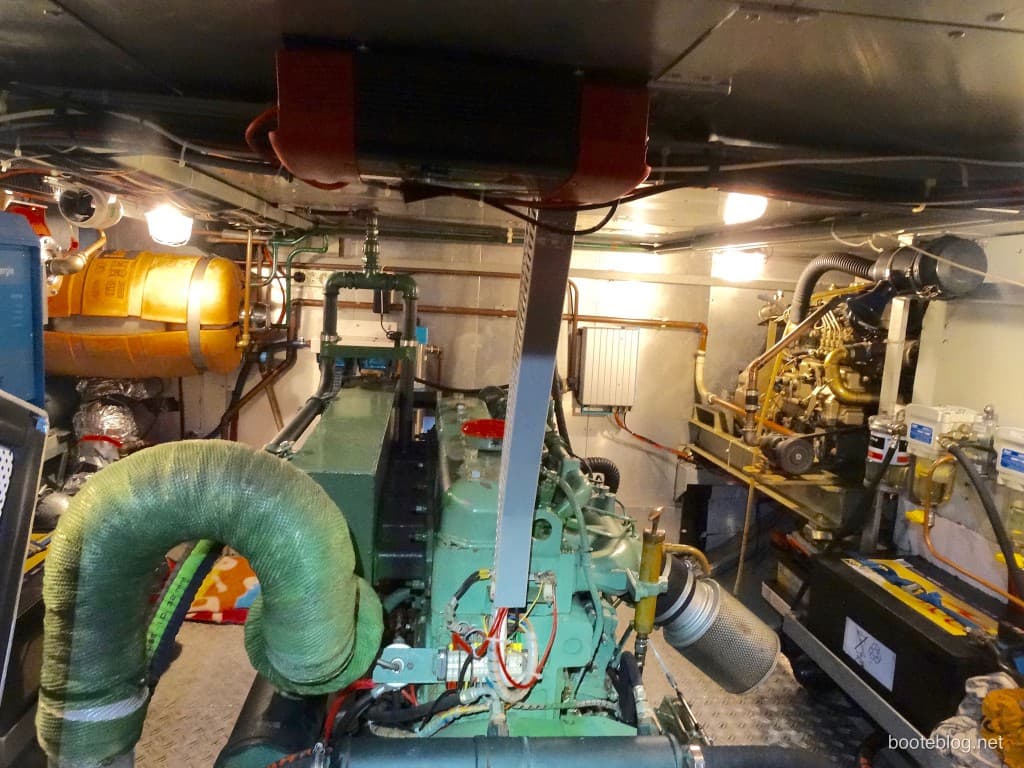
Rohre, Kabelkanäle, Aggregate überall – und eine Schallisolierung muss so lückenlos wie möglich installiert werden. Also war abzusehen, dass ich viel messen und zuschneiden musste, um das Material möglichst eng an diesen Unebenheiten anzubringen (ganz perfekt wäre es natürlich, alles abzubauen, Material aufzubringen und wieder anzubauen – aber so verrückt bin nichtmal ich!).
Also ging die Arbeit mit Zollstock, Stift und Stichsäge los:
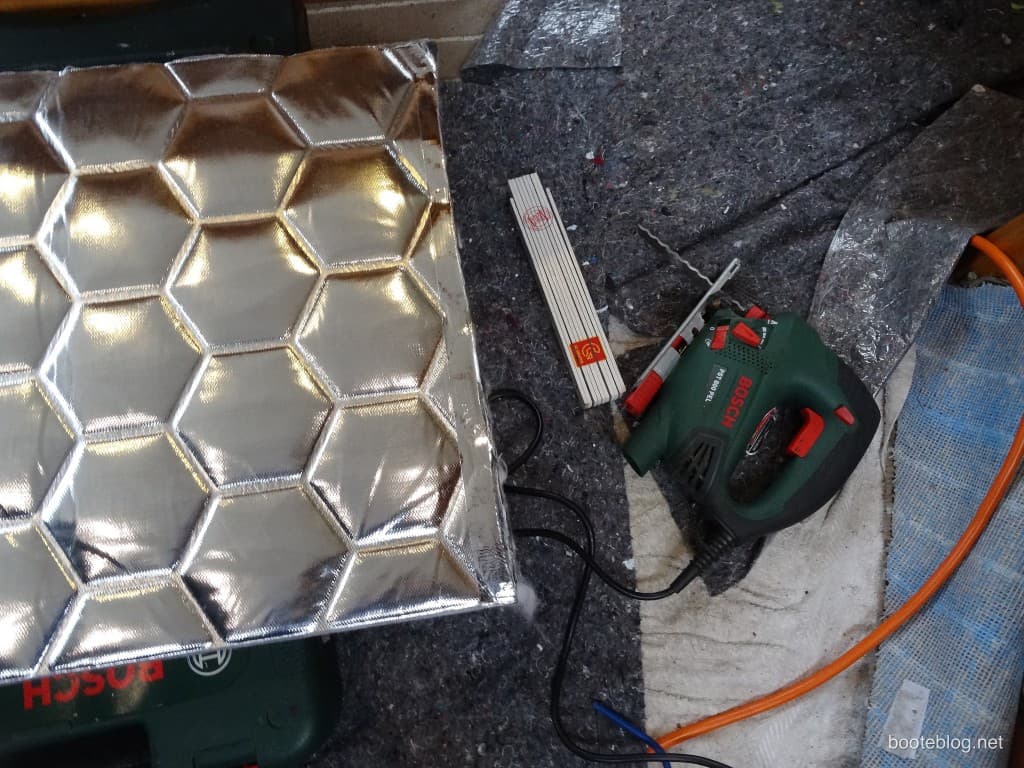
An der Stichsäge hatte ich ein Messer, das es auch bei Recytex gibt, montiert – und das ist unbedingt zu empfehlen! Mit einer scharfen, großen Schere geht es theoretisch auch, ist praktisch aber eine erhebliche Kraftanstrengung!
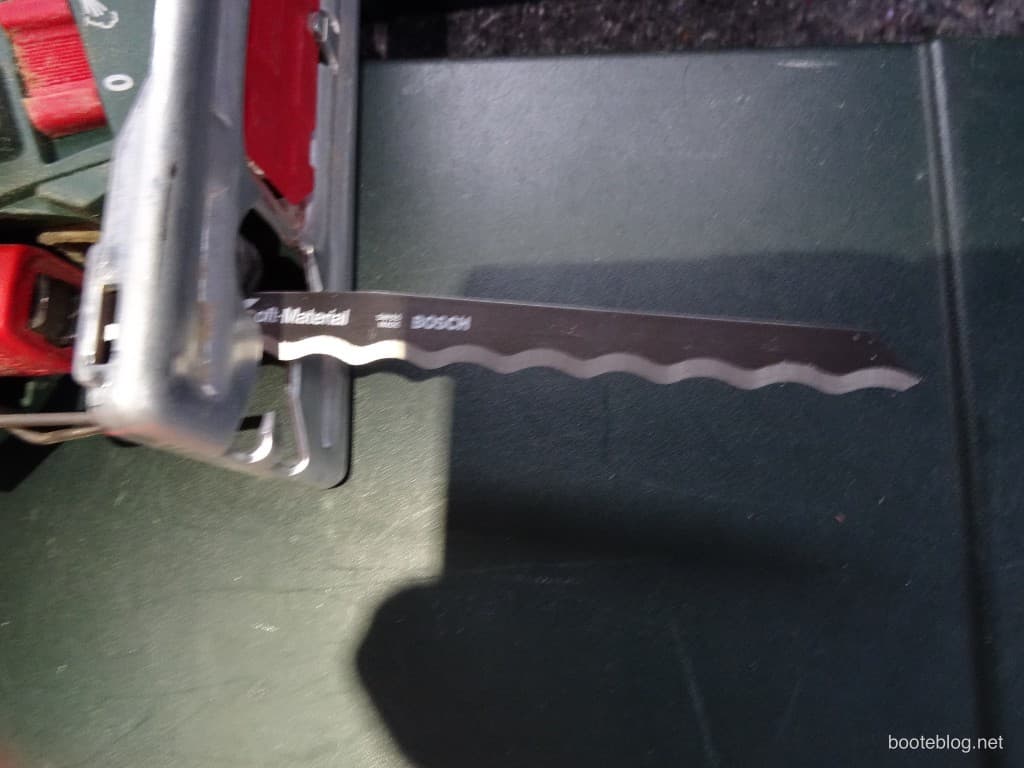
Ungefähr 20 Arbeitsstunden später glänze und glitzerte die neue Schallisolierung im Maschinenraum:
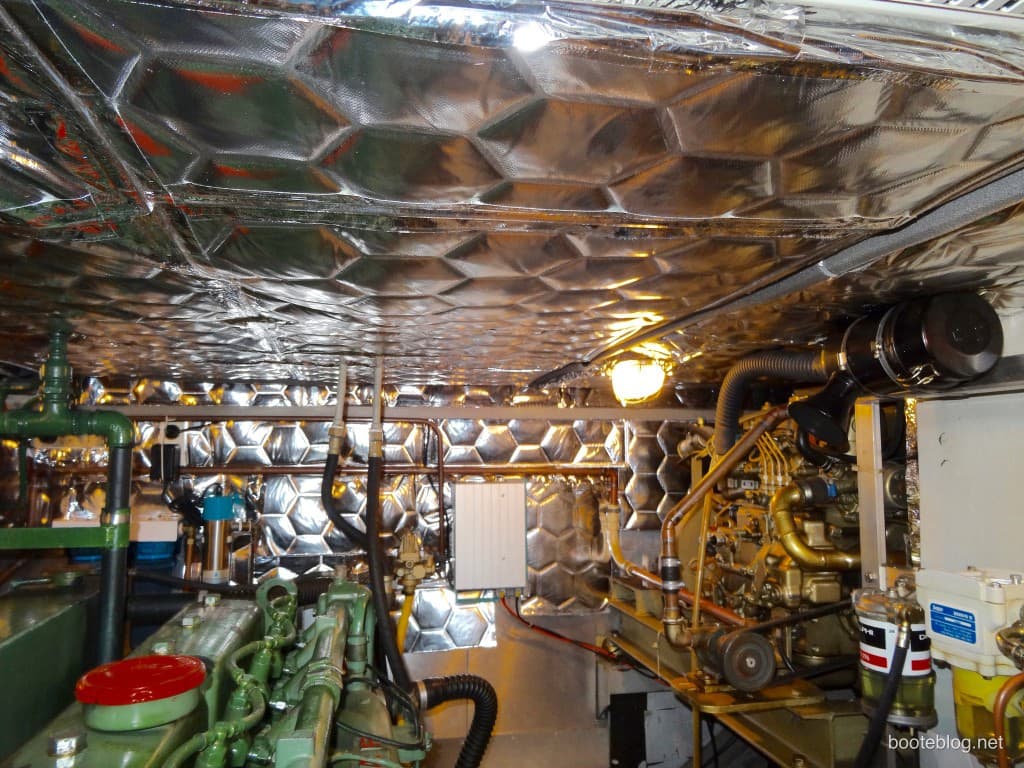
Dazu ein paar Stichworte:
- Der Kleber an den Matten macht genau das, was er soll: Er klebt. Stark. Sehr, sehr stark. Daher immer erstmal nur ein Stück der Schutzfolie abziehen, die Matte positionieren und mit der ungeschützten Klebestelle fixieren. Dann erst nach und nach den Rest der Folie abziehen und die Matte andrücken.
- Je stärker angedrückt wird, desto besser hält der Kleber.
- An der Decke scheinen (!) die Matten auch ohne mechanische Fixierung zu halten. Genau weiß ich das aber erst in einigen Monaten.
- Der Untergrund muss vorher mit einem fettlösenden Mittel geputzt werden und dann völlig trocken sein.
- Schnittkanten können und sollten (!) mit dem Dekorklebeband abgeklebt werden. Schätze, wie viele Rollen du davon brauchst und bestelle dann die doppelte Menge.
- Die Wände sind mindestens so wichtig wie die Decke. Die Wand im Foto konnte ich mangels Material nicht mehr komplett bedecken (was ich wohl im Herbst nachholen werde…).
Was hat es gebracht?
Höre einfach selbst. Ich habe die laufende Maschine vom inneren Fahrstand aufgenommen. Hier ein Zusammenschnitt davon: Bei 1000 Umdrehungen, die 6,5 Knoten Fahrt entsprechen. Zuerst 10 Sekunden im Ursprungszustand, dann nachdem ich das Recytex-Material aufgebracht habe.
Und, wie stark empfindest du den Unterschied?
Ich war zuerst enttäuscht und hatte mir deutlich mehr erwartet! Daher betrieb ich Ursachenforschung: Sehr gutes (und teures!) Material, so lückenlos verarbeitet wie möglich – warum ist der Unterschied nicht deutlicher?
Lessons learned
Dazu habe ich mit einer iPad App das Maschinengeräusch bei geschlossenem Maschinenraum, also mit voller Wirkung der Schallisolierung, hinsichtlich der Frequenzverteilung analysiert:
Hier spielt ich das Maschinengeräusch also fast nur im Bereich bis 2000 Herz ab, mit Spitzen zwischen 200 und 400 Herz sowie 1200 und 1400 Herz Ab 2000 Herz fällt der Pegel stark ab, und ab 2400 Herz ist fast kein Schallpegel mehr vorhanden.
Im Gegensatz dazu ist der Lärm bei geöffneter Tür zum Maschinenraum über den ganzen Frequenzbereich fast gleich laut (leider habe ich davon keinen Screenshot)!
Die Schallisolierung leistet also Erhebliches! Aber eben hauptsächlich im mittleren und hohen Frequenzbereich. Genau das ist in der Tonaufnahme auch zu hören: Nach der Isolierung enthält das Maschinengeräusch deutlich weniger mittlere und hohe Töne. Aber was ist mit dem niederfrequenten Schall?
Schall in den niedrigeren Frequenzen hat wesentlich mehr Energie, und ist daher viel schwieriger aufzuhalten. Das geht nur durch Masse, und dafür ist das Material wohl nicht schwer genug.
Dazu kommt der Körperschall: Die Maschine überträgt vor allem niederfrequente Geräusche auf den Schiffskörper, der ihn dann überall im Schiff abstrahlt und wieder in hörbaren Schall wandelt.
Somit muss ich wohl anerkennen, das ich die maximal mögliche Schallisolierung im Maschinenraum so gut wie erreicht habe. Leiser wird es nicht. Natürlich kann ich noch hier und da an den Wänden Material aufbringen, das dient dann aber eher der Vollständigkeit der Optik und wird zur Schallreduzierung wenig beitragen.
Einen deutlich hörbaren Unterschied wäre nur möglich durch:
- Vollständige Auskleidung des Maschinenraums ohne Aggregate, Rohre und Kabelkanäle – also perfekt lückenlos.
- Austausch der Maschinen-Fundamente durch spezielle Fundamente, die akustisch möglichst perfekt entkoppelt sind.
Aber wie oben schon erwähnt: So verrückt, das umzusetzen, bin nichtmal ich.
Anmerkungen von Michael Herrmann (Fachautor von yachtinside.de)
Lärmreduzierung im Schiff besteht – wenn sie denn Wirkung zeigen soll – immer aus mehreren Maßnahmen. Einerseits soll mit Schalldämmung der Lärm nicht aus dem Maschinenraum entkommen, was üblicherweise mit Masse am besten funktioniert, während gleichzeitig der Lärm im Maschinenraum mit Schalldämpfung in Wärme oder andere Energieformen umgewandelt werden soll.
Erst durch die Verbindung dieser beiden Maßnahmen ist eine wirkungsvolle Lärmreduzierung möglich.
Weitere, scheinbar nicht so leicht beeinflussbare Faktoren sind der Primärschall, also der Krach, der vom Motor produziert wird und der vom Motor in den Rumpf eingeleitete Körperschall, der an anderen Stellen im Schiff wieder in Luftschall zurückverwandelt wird. Soweit die Lage.
Eigenheiten des menschlichen Gehörs
Jetzt kommt der Mensch in’s Spiel: Unser Gehör kann Schall über einen unglaublich weiten Intensitätsbereich wahrnehmen – Schalldruckpegel von 10 hoch minus 12 bis 1 Watt/qm – ein Verhältnis von 1:1 000 000 000. Um hier nicht dauernd mit ewig langen Zahlen rechnen zu müssen, werden Schalldruckpegel und Schallleistungen in der logarithmischen Einheit „Bel“ beziehungsweise Dezibel angegeben.
Damit lässt sich der gesamte Hörbereich mit 3-Stelligen Zahlen angeben, zum Beispiel 0 (Hörgrenze) bis 120 dB (Schmerzgrenze). Diese Zusammenhänge sind nicht ganz einfach, so dass sich mit der Zeit einige Legenden bildeten.
Aufräumen mit Legenden
Ich versuche ein wenig Aufklärung: Die Schallleistung einer Schallquelle – beispielsweise Motor – ist eine Energiegröße und zunächst unabhängig von irgendeiner Entfernung. Sie ist die gesamte von dem Motor abgegebene Schallemmission, sagen wir 110 dB. Dies ist die gesamte Schallleistung, die der Motor abgibt, unabhängig von irgendwelchen Entfernungen.
Eine Reduzierung dieser Leistung um 3 dB entspricht dann einer Halbierung (der Motor wird „leiser“), was gerade eben als Lautstärkeunterschied wahrnehmbar ist, jedoch keinesfalls einer Halbierung der subjektiv empfundenen „Lautheit“ entspricht. Dazu bräuchte man hier eine Reduzierung um 10 dB – das heißt, auf ein Zehntel der ursprünglichen Leistung. Erst das Verhältnis 1:10 wird vom Gehör als Halbierung wahrgenommen.
Bei der Feldgröße „Schalldruckpegel“ verdoppeln sich diese Differenzen, da es sich hier um eine Feldgröße – die Ausbreitung des Schalls im Raum – handelt. Diese Größe bewegt sich im Raum und nimmt mit der Entfernung ab. Eine Verdoppelung des Abstands zur Schallquelle führt hier zu einer Reduzierung um 6 dB – was man gut nachvollziehen kann, wenn man sich den sich ausbreitenden Schall als Kugel vorstellt.
Apamat-Messung? Wenig aussagekräftig!
Diese unterschiedlichen Eigenschaften von Schallleistung und Schalldruckpegel ist auch einer der Gründe, weshalb die (nicht standardisierte) „Apamat-Messung“ der Lärmdämmung alleine nicht aussagekräftig ist und zu überhöhten Erwartungen führt – es wird nicht zwischen Schallpegel und Schallleistung unterschieden, und wir wissen nicht, um welche „Lärmart“ (zum Beispiel Terzrauschen oder weißes Rauschen) es sich handelt.
„Stahlkugeln auf einer Blechplatte“ ist zwar eine anschauliche Beschreibung, jedoch nicht unbedingt für einen objektiven Vergleich geeignet. 24 dB Reduzierung des Schalldruckpegels im mittleren Frequenzbereich sieht dann auf dem Papier gut aus, unsere Ohren lassen sich jedoch meist nicht so leicht beeindrucken. Oder anders: Selbst wenn der Schalldruckpegel um das 100-fache gesenkt wird (20 dB), wird dies immer noch als „halb so laut“ wahrgenommen – was bei rund 110 dB Motorschallleistung immer noch 90 dB sein können.
Tiefe Frequenzen und Tipps für die Praxis
Zu den tiefen Frequenzen: Diese werde in der Regel über die Schwingelemente der Motorlagerung in die Fundamente und damit den Rumpf eingeleitet. Hier kann – je nach Ausgangslage – oft eine deutliche Reduzierung der Übertragung (>6 dB) durch angepasste Schwingmetalle erreicht werden.
Für die Praxis: Schalldämmung ist primär eine Funktion des Flächengewichts der Wände und Decken um die Schallquelle (doppeltes Flächengewicht = 6 dB Dämmung),
Dämpfung ist eine Funktion der Resorption von Schall durch entsprechende Oberflächen oder Resonanzflächen. Kleinste Luftschallbrücken können jedes noch so teure Schalldämmmaterial austricksen, und Körperschalleinleitung kann oft mit verhätnismäßig einfachen, jedoch nicht unbedingt billigen, Maßnahmen reduziert werden.
Selbst Primärschall kann oft alleine schon durch den Einsatz eines Ansauggeräuschschalldämpfers („Luftfilter“) aus dem KFZ-Bereich reduziert werden. Wir haben damit rund 6 dB erreicht. All das lässt sich aufgrund der praktischen Einheit „Dezibel“ bequem aufaddieren, will man die Wirkung von Schalldämmmaßnahmen vorher abschätzen.
Diese Anmerkungen stammen vom Fachautor Michael Herrmann, der sein gesammeltes Fachwissen auf dem sehr empfehlenswerten Angebot yachtinside.de publiziert.
Hallo Julian!
Sehr interessant!
Was die Dämmung der tiefen Frequenzen angeht, die, wie Du schon früher bei der Xenia schriebst, nur durch Masse (Gewicht) abzudämmen sind, wie ist denn das Gewichtsverhätlnis zwischen den AIXFOAM-Matten und dem jetzt verwendeten Material RECYTEX? Gibt’s da Unterschiede – oder sind die annähernd gleich?
Irgendwann muss ich auf meinem Boot da nämlich auch ran….
Gruß
Hallo Volker,
aus meiner Erinnerung ist das SH0071 in 50mm einen Tick schwerer als das Recyguard W600. SH0071 gibt es auch mit Schwerfolie, dann ist es garantiert schwerer und dämmt tiefe Frequenzen wahrscheinlich besser.
Aber: je schwerer das Material, desto unwahrscheinlicher ist es, dass es nur durch die Klebung an der Decke hält – SH0071 mit Schwerfolie würde ich nur mit mechanischer Sicherung verwenden.
Recytex hat auch noch dickeres Material, W1300 glaub ich heißt das. Das ist noch teurer, hat aber die tolle Oberfläche, die ich bei dem SH0071 von Aixfoam vermisse.
Ein Kompromiss könnte SH0081 von Aixfoam mit Schwerfolie und Alu-Kaschierung sein – wie belastbar die Oberfläche ist weiß ich aber nicht.
Danke!
Hallo Julian!
ich bins noch mal. Noch eine Frage: Wie heisst die iPad App, die du benutzt hast.
Ich habe ein Android Tablet und suche mich tot im Gugl Playstore.
Vielleicht gibt es deine App ja analog auch für Android.
Danke!
Volker
SpectrumView von OxfordWaveResearch: http://www.oxfordwaveresearch.com/j2/products/spectrumview
Gibts aber nur für iOS 🙂
OK, DANKE.
Jetzt weiss ich wenigstens, wonach ich suchen muss: Spektrum-Analyse oder so ähnlich. Schuan mar mal.
V.
Interessant zu lesen.
Ich muss auch mal wieder messen, was meine Maßnahmen zur Motorschalldämmung nun effektiv gebracht haben.
Ich hatte damals bei Sontech in Dordrecht, die u.a. in Motorraumisolierung von Schiffen spezialisiert sind, angerufen und mich beraten lassen.
Wie Du bereits feststellst: die tiefen Frequenzen sind wichtig!
Ich habe auf Grund ihrer Empfehlung die Wände des Maschinenraum erst mit Schwerfolie
Sonomass von sontech.nl: Kunstoffmatten auf Basis EPDM
„Gewicht ist vergleichbar mit Bitumen. Stärke 7,2 mm = 14 kg/m² , besonders geeignet für dickere Schiffshaut.“
beklebt (auch Decke) und darüber dann AIXfoam, 50 mm angebracht.
Kann leider zur Zeit keine Schallmessung machen, da ich wegen Aufräumarbeiten etc. den Startakku abgeklemmt habe.
Werde das aber in der nächsten Woche nachholen.
groetjes Norbert
Hallo Norbert,
Hast du das aixfoam Material mit Oberflächenkaschierung? Wenn ja, wie stabil ist die? Kann man da zB mit einem Kugelschreiber durchstoßen?
Hallo Julian,
ich habe AIXFoam SH0071 verbaut. Die Sonomass Platten sind mit Kleber (wie Pattex) auf die Schiffshaut bzw. die beiden Schotten geklebt und dann den selbstklebenden AIXFoam drauf. An der Decke klebten die Sonomass platten prima, den AIXFoam habe ich zusätzlich in jeweils ca. 20 cm Abstand mit langen Holzschraube mit großer Unterlegscheibe am Kopf gesichert.
Die Platten-Stärke von 50 mm kam gut aus weil meine Spanten – die Schiffshaut ist auf genietet – etwa 50mm hoch sind.
Eine glatte Außenhaut und dann noch im schicken Silberlook fand ich damals auch schöner – bzw. hellt den Maschinenraum zusätzlich auf.
Warum ich dann doch die nicht kaschierten Platten gekauft habe weiß ich nicht mehr.
Ich habe damals vor der Isolierung Schallmessungen gemacht.
Was es jetzt gebracht hat kann ich noch nicht sagen. Die Luke, durch die ich in den Maschinenraum steige habe ich nämlich bisher noch nicht angepasst/isoliert. Steht auf der to-do Liste.
Danke für die Infos, das ist bestimmt ein ziemlich effektiver Aufbau. Ich würde mich freuen, wenn Du hier noch mal schreibst wenn Du das Ergebnis hast!
Im nachhinein hätte ich wohl auch zuerst Schwerfolie (gibts auch bei Aixfoam einzeln) aufbringen sollen, und dann darauf das Recytex Material. Aber nun ist’s zu spät, und ich klage ja auch auf sehr hohem Niveau 🙂
Servus,
hat es schon mal jemand mit aktiver Geräuschdämmung versucht?
Stichwort Gegenschall.
LG Jens
ich hab mich mal ein wenig damit beschäftigt, der Aufwand schien mir aber zu hoch… letztlich muss da eine ganze Menge Schallenergie erzeugt werden, und die Energie muss ja irgendwo herkommen, sprich: so eine Lösung hat meinen Recherchen nach einen spürbaren Stromverbrauch.
Moin,
ok. Ich dachte nur, da solche Anlagen inzwischen schon in Autos verbaut werden, das es sowas doch für Motorboote geben muss.
LG Jens
Hallo
Hat auch jemand einen Tip, was man gegen lärm von aussen machen kann.
schon kleinste Wellen machen es mir unmöglich in meinem Boot (SBM600) zu schlafen.
Gruß Carsten
Hallo Carsten,
es gibt große, aufblasbare Schläuche die man ums Boot legen kann um Wellen abzuhalten. Ob die was bringen? Keine Ahnung, ich bezweifel es. Meine Empfehlung ist da eher, Ohrstöpsel zu verwenden… ich nutze die von Hansaplast und komme damit sehr gut zurecht (Link findest du hier: http://booteblog.net/2016/06/26/was-sich-bewaehrt-boot-erfahrung-ostee-nordsee/). Damit sind die Geräusche alle sehr gedämmt, aber trotzdem hört man noch was.
Bauliche Maßnahmen am Boot, um Wellengeräusche zu verhindern, sind mir nicht bekannt.
Erstmal danke für die Antwort.
Ich dachte eher an ein isolieren der Bordwand von innen.
Leider ist mein Boot nur einwandig und deshalb dachte ich eher an ein isoliern von innen.
Mein Gedanke ist das auskleben mit Alubutyl (Antidrönmatte) und darauf eine Schicht Dämmschaummatte.
Vielleicht hat ja jemand dami Erfahrung.
Geuß Carsten
Hallo Julian,
ich habe meinen Stahlverdränger durch eine Elling E3 ersetzt.
Das Schiff ist generell schon relativ leise aber der Schaumstoff im Maschinenraum ist eher von der einfacheren Sorte und jetzt auch schon 20 Jahre alt.
Hast Du ein Fazit welchen Schichtaufbau Du für ideal oder noch besser halten würdest und welchen Hersteller?
In den Kommentaren hattest Du ja schon erwähnt evtl. doch besser zuerst Schwerfolie zu nehmen und dann den Schaumstoff.
Vielen Dank und viele Grüße, Christian
Hallo Christian,
Glückwunsch zur Elling
Wenn du großflächige Bereiche hast ist die Schwerschaumfolie und darauf SH071 von Aixfoam sicher eine gute Wahl. Der Maschinenraum der Elling ist ja kein Raum im eigentlichen Sinne, sondern vom Lebensbereich umschlossen und durch große Klappen zugänglich wenn ich mich richtig erinnere?
Dann wäre die tolle Oberfläche von Recytex vielleicht verzichtbar.
Oder ruf mal bei Aixfoam an und frage, ob für diesen Zweck deren Material mit Oberflächenkaschierung geeignet wäre und ähnlich gute Werte wie SH071 erzielt.
Recytex kannst du an der Decke nur mit zusätzlicher mechanischer Sicherung aufbringen. Zumindest bei mir haben sich die Platten an der Decke nach und nach irgendwo im Verbund gelöst und ich musste nachkleben.
Viel Erfolg und berichte mal, was du genommen hast!
Hallo Julian,
ok, danke für die schnelle Nachricht.
Mit dem Maschinenraum hast Du Recht, ist quasi komplett gekapselt. Im Steuerhaus habe ich bei Marschfahrt ca. 69dB.
Da die Flächen alle schon gedämmt sind sollte es eigentlich nicht schwer sein das Ganze zu verbessern.
Wird aber noch bis in den April dauern da ich das Boot erst dann abhole.
Hast Du Dir damals auch die Ellings angeschaut oder wolltest Du auf jeden Fall beim Stahl bleiben?
Hallo Julian,
besten Dank für den sehr interessanten und v.a. mit Messdaten hinterlegten Bericht. Ich habe mit diesem Recytec Produkt folgende Erfahrung gemacht: Sehr gute Schalldämmung, sehr schlechter Geruch! Anwendungsfall war hier das Gebläse für die Heizung und Lüftung der Kabine. Der Axial-Lüfter (Pabst) hat bis zu 400 Watt und bläst bei Volllast mit fast 100 km/h. Entsprechend laut ist das Geräusch. Daher habe ich:
1. den Lüfter an ein Brett montiert, das nur mit einer Schraube an einer Ecke befestigt ist (Minimierung Körperschall)
2. den Lüfter mitsamt Wärmetauscher in einem eigenen Raum gekapselt (zwischen Tank und Motorraum), Volumen ca. 100 Liter)
3. diesen Raum mit ebendiesem Recytex ausgekleidet.
4. nach diesem Raum noch einen längeren Kanal angebracht, der ebenfalls gedämmt ist, allerdings mit billigerem Recytex.
Ergebnis: Vom Lüfter hört man selbst bei Volllast fast nichts mehr. ABER: Es stinkt! UNd zwar gerade das teuere Material. Es riecht muffig und chemisch. Zunächst hatte ich eine tote Maus im Verdacht und habe alles wieder zerlegt. Es war aber das Dämmmaterial. Das Fatale ist: Bis dieser Geruch verflogen ist, muss die Lüftung locker eine Stunde laufen (natürlich nicht in Vollast, sondern nur mit ca. 25%). Sobald man die Lüftung für ein paar Stunden abstellt und dann wieder einschaltet: Gleiche Situation. Und zwar seit Jahren! Ich habe das Material in 2013/14 installiert. Bis heute dünstet also irgendwas aus.
Mich würde interessieren, wie es bei Dir riecht. Und ob jemand ähnliche Erfahrungen gemacht hat.
Beste Grüße
Georg
Interessanter Anwendungsfall 😀 Zum Geruch kann ich nichts sagen, bei mir lebt das Material ja im Maschinenraum, und dort ist ohnehin permanenter Luftaustausch nach außen hin. Ich gehe immer nach abstellen der Maschine in den Maschinenraum, um das Seeventil zu schließen. Dann sind die Lüfter häufig aus, ein unangenehmer Geruch ist mir dabei noch nie aufgefallen.
Vielleicht hat es bei dir was mit Temperatur zu tun? Wie warm ist es denn an den Stellen wo das Recytex Material angebracht ist? Bei mir im Maschinenraum sind nach ein paar Stunden fahrt knapp 40 Grad.
Hallo Julian,
das ist wieder mal ein interessantes Video (Update Schallisolation 2023) zu diesem nicht minder interessanten Thema.
Das im Video erwähnte Aluband mit der überstehenden Folie gibt es zum Beispiel von Recytex in 5 und 10 cm Breite:
https://recytex-shop.de/de/montagezubehoer/21-kantenband-alu-10cm.html
Viele Grüße
Hendrik
Hendrik, danke für den Hinweis und Link!